Are you understand?
On my desk the following day was this note:
It was attached to a piece of paper that looked like a can of Japanese had been shaken up and sprayed on it.
Am I understand?
No I'm not.
Before I had a chance to delve too deeply in my new "assignment" the tour guide from yesterday gave me a stack of xeroxed pages that I now take to be the training manual. I'm as understand of this as I was of the other thing. My lack of understanding was compounded by the fact that some pages of this document were copies of copies of faxes of copies. Think it's tricky making out all those little Japanese characters when they're clear? Tour Guide was nice enough to write out the pronunciation for the pertinent ones. This makes it much easier to bang them into my little electronic dictionary and get some of that sweet, sweet English in return. It was a testing checklist for a typical part. Minimum thickness after processing. Hole size +- 0.2mm. I spent another hour on that first page that was left on my desk and called it a day.
The next day had me doing some actual work. I put on my blue cap and went to the quality check room. There a guy whose name sounds like Hogarth showed me the ropes. I can't say I understood what was said, but checking a part's quality consists mostly of measuring thiknesses and widths with a little miracle device called a micrometer . This seemed easy enough, but I was started on even more basic stuff. A bin of little doohickies came in. For the first round I was to forego the micrometer and just make sure that each part had two holes, two nuts, and a bolt. I'm sorry, but that's what it was. And guess what, they all did.
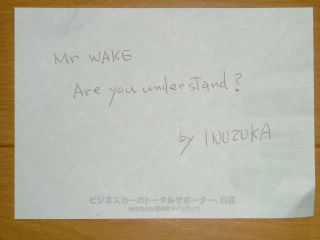
It was attached to a piece of paper that looked like a can of Japanese had been shaken up and sprayed on it.
Am I understand?
No I'm not.
Before I had a chance to delve too deeply in my new "assignment" the tour guide from yesterday gave me a stack of xeroxed pages that I now take to be the training manual. I'm as understand of this as I was of the other thing. My lack of understanding was compounded by the fact that some pages of this document were copies of copies of faxes of copies. Think it's tricky making out all those little Japanese characters when they're clear? Tour Guide was nice enough to write out the pronunciation for the pertinent ones. This makes it much easier to bang them into my little electronic dictionary and get some of that sweet, sweet English in return. It was a testing checklist for a typical part. Minimum thickness after processing. Hole size +- 0.2mm. I spent another hour on that first page that was left on my desk and called it a day.
The next day had me doing some actual work. I put on my blue cap and went to the quality check room. There a guy whose name sounds like Hogarth showed me the ropes. I can't say I understood what was said, but checking a part's quality consists mostly of measuring thiknesses and widths with a little miracle device called a micrometer . This seemed easy enough, but I was started on even more basic stuff. A bin of little doohickies came in. For the first round I was to forego the micrometer and just make sure that each part had two holes, two nuts, and a bolt. I'm sorry, but that's what it was. And guess what, they all did.
0 Comments:
Post a Comment
<< Home